Hoffman Builds the Largest Fab To‑Date to Deliver the Next Generation of Processors
Fab 42
Hoffman built this advanced fab for one of the world’s largest makers of microchips; it is the first production facility for the next generation of processors.
At the time of its construction, Fab 42 and its sister fabs (including Hoffman’s D1X) were the largest fabs the owner had built. The 1,300,000 SF plant features 240,000 SF of cleanroom space, (562,000 SF gross that includes ancillary clean non-production spaces) a process utility building (PUB), a boiler-chiller plant (BCP), and a fab support building (FSB) with labs and other facilities. A general purpose building (GPB) adds a cafeteria and other office/support space for people working in the fab. The workforce exceeded 4,000 workers and used 120,000 CY of concrete and 12,000 tons of structural steel. The fab was completed in 16 months.
Pouring concrete through a hot Arizona summer necessitated special techniques, including 1 AM pours and using ice in the concrete mix. Hoffman pioneered new modular and prefab construction processes to deliver this project. We built utility racks on the floor and raised them into place using screw jacks like those used to lift airplane wings and fuselage sections into place. Large portions of the pipe racks and assemblies were built in shops off-site, reducing congestion inside the new factory.
Pre-assembled components were shipped to the site and installed in racks. Each finished rack was 166’ long and weighed over 180,000 pounds. Extensive collaboration between Hoffman, the jack maker, and the engineers who implemented this innovation resulted in cost savings of > $25M, schedule improvements of 60%, and 90% reduction in overhead work.
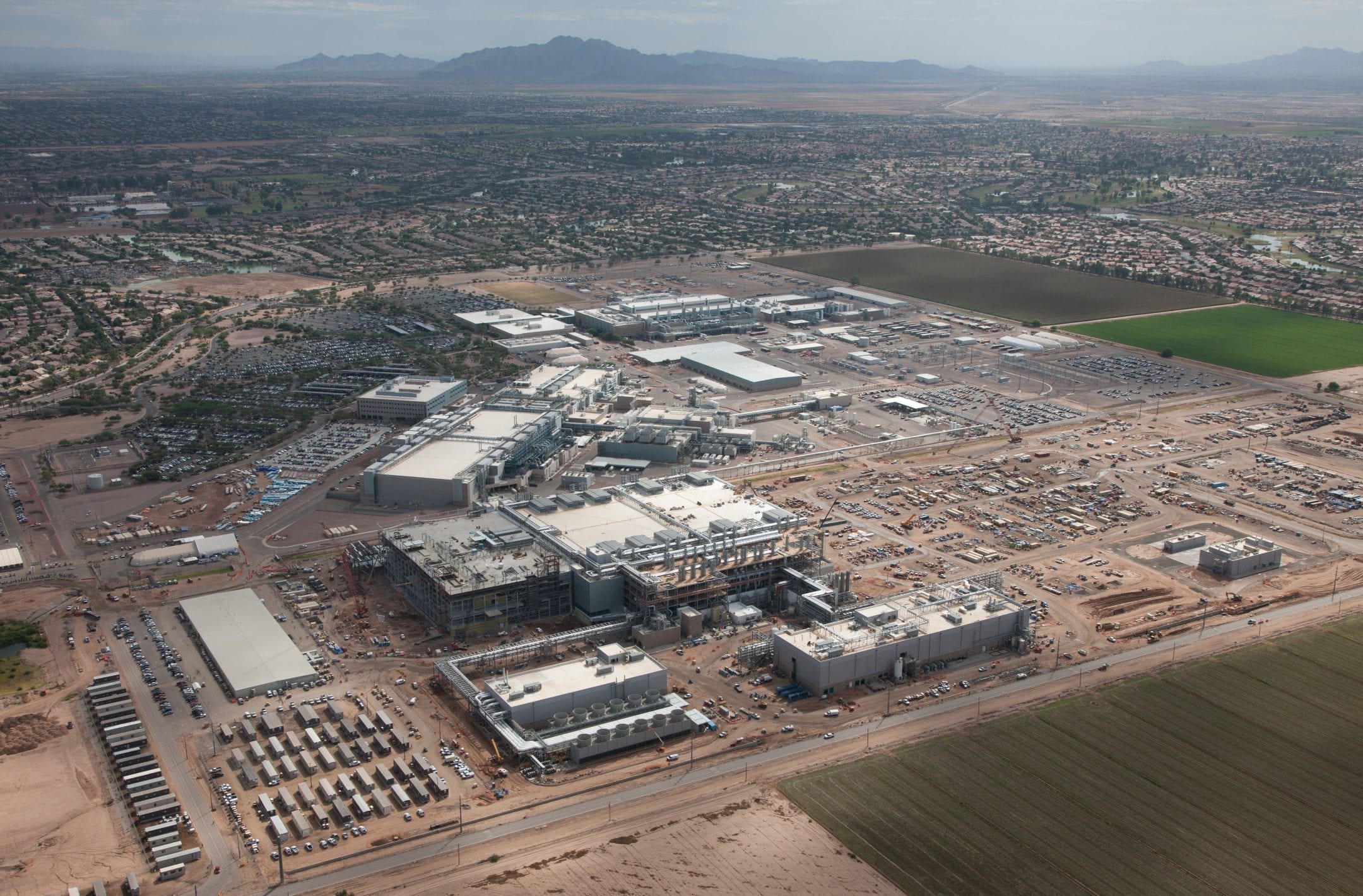